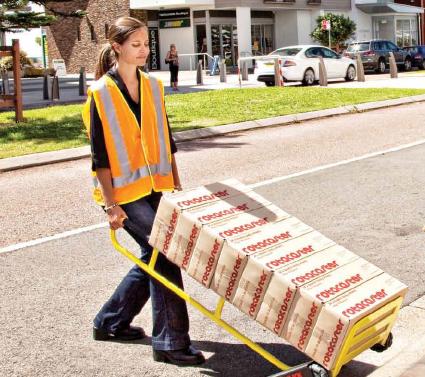
Thomas R. Cutler describes the advantages of the omniwheel, the revolutionary alternative to the swivel caster, and heralds the entry of Rotacaster into the next dictionary.
The Kleenex brand is synonymous with tissues. Other brands, like Hoover, have dominated the market to such an extent at times that they have entered the dictionary to describe the concept itself. You don’t search for something online, anymore. You Google it.
For a century the basic caster wheel has changed little and no company or brand has claimed the caster nomenclature, until now. The omniwheel is the generic name; Rotacaster is the brand.
Omniwheels, defined in Wikipedia, are sometimes called poly wheels, and have small discs around the circumference which are perpendicular to the rolling direction. The effect is that the wheel will roll with full force, but will also slide laterally with great ease. These wheels are often employed in holonomic drive systems.
360 degree maneuverability without turning or swiveling wheels is a clear differentiation. Looking more closely at this innovative product, data among users revealed better directional control and tracking, precise positioning - without swivel offset correction, and no resistance due to misaligned swivel castors. Rotacasters require minimal wheel space or /housing requirements and simple mounting allows the ability to choose from forks, cups, channels and rails or stack together on an axle to form a roller wheel.
Load stability is vital in the industrial and distribution environment and requires a static center of load relative to wheel base; load distribution is achieved providing the ability to use multiple wheels without swivel offset resistance as well as the capacity to tilt or lever off the fixed wheel mounting. The next generation of omniwheels has to be tough, manufactured from engineering grade polymers; the conditions on a plant floor require a rust free, full polymer construction with no steel pins and non-marking polyurethane rollers.Corrosive environments are often found on the plant floor as well as the need for x-ray or scanning applications.
Rotacaster's unlimited maneuverability makes it a real alternative to a swivel caster and brings a whole new dimension of possibility to the design and functionality of wheeled products. Peter McKinnon, managing director of the Australian company, noted, “Durable construction, high load bearing capacity, stable mounting capabilities and smooth ride quality make Rotacaster multidirectional wheels suitable for tough environments and industrial applications. The innovation takes an age old concept and puts a new twist on it, developing a true alternative to the swivel caster.”
The original concept for the Rotacaster multi-directional wheel was developed by founder, Henry Guile, whose inspiration came from the Bible. The first chapter of Ezekiel describes a vehicle with four wheels and “their appearance and their work was as if it were a wheel in the middle of a wheel.” From this simple idea, the Ezekiel Wheel was born.
Guile worked on his wheel for many years, but his dream was never fully realized. Many years later his son Graham revisited his father’s early work, re-engineering the wheel into the Rotacaster wheel of today - a sturdy, robust wheel, adaptable to a vast array of applications and the solution to the many shortfalls of the traditional swivel caster.
The Rotacaster wheel combines the freedom of 360 degree movement with the stability of a fixed mounting, achieved through a patented design and monolithic, web-like construction which uses rollers rather than a swivel mount. Sold throughout Australia and exported around the world, the Rotacaster is used as a floor wheel, a conveyor wheel and in applications such as hand carts and trolleys, material handling equipment, robotics, mobile furniture, pipe rollers and as an alternative to ball transfer units.
While multi-directional wheels have been used for some time in conveyor and light-duty robotics applications, the Rotacaster wheel is engineered to provide the additional durability and ride quality necessary for use as an industrial floor wheel. Manufactured from engineering polymers, Rotacaster injection-molded wheels have no pins, inserts or seams, making them ideal for tough environments. The fixed orientation of the wheel facilitates both simple and stable mounting alternatives that improve load stability and are less prone to impact damage. This also allows for the wheel to be housed within a product with minimal space or clearance requirements.
Multi-directional conveyor transfer wheels are built to provide the ride quality of an industrial floor wheel; simple mounting options make them easy to adapt to existing systems and injection molded cup mounts provide the perfect alternative to a ball transfer unit. Unlike standard swivel casters, the Rotacaster’s compact size allows more wheels per m² and minimal spacing between adjacent rollers for greater load distribution, reduced soft surface indentation, and the ability to handle a greater range of surface profiles.
Improving productivity with this revolutionary design is achieved through better impact resistance, higher load capacity, and reduced risk of downtime due to lost rollers. According to David Dosier, product manager for Magnus Mobility, the North American distributor of Rotacaster, “There will be a dramatic increase in Rotacasters because it is a simple, fast mounting alternative, lighter and stronger than similar wheels, and provides a quieter and smoother ride.”
Quality managers and operations managers evaluating the choices of roller options want protection of surfaces, greater traction for driven applications, and the ability to adjust for different climatic environments.
McKinnon has seen the real world applications of the Rotacaster expand rapidly from material handling equipment (hand trucks, trolleys, dollies, carts, skates) to shopping carts and luggage, freezer duty trolleys and carts as well as conveyor transfers, pipe rollers and other inverted applications. Recently the wheel has also been used for ball transfer table alternatives for mobile furniture, appliances and work benches, as well as robotics.
Productivity and process improvements of the delivery componentare driving most supply chain and automation changes across industry. Delivery is a vital step in the value chain because themerchandise is handled in a packaging format that requires the use of hand trucks.
Firms offering solutions toautomate delivery requirements and address stackable merchandisewill see dramatic sales improvements in 2012. A tall, heavyload magnifies the force placed on the frame, axles, wheels and bearings of the handtruck which leads to breakdowns and repairs. Of equal or greater concern is the fact that the hand truck status quo requires the hand truckoperator to exert significant effort in pulling back, supporting and maneuvering the load.
Dosier detailed some of the specific challenges in these types of material handling situations, noting “Uneven surfaces, long distances, and physical obstacles are real issues impacting the delivery supply chain. The amount of uneven surface area covered magnifies the impact of stress on theoperator’s body and on the hand truck. Uneven surfaces also eliminate the ability to uselarger delivery trucks that can also fully support the load.”
The typical range of distance traveled from the ramp of the truck to the delivery area ofthe retail storefront is 10ft to 100ft. When the distance traveled is significantly increased, such as 100 to 400 yards for mall and casino deliveries, the company tendsto use a differenttype of hand truck.
“Negotiating curbs, changing levels or thresholds, traversing doorways and lift entrancesall require additional activity and exertion to ascend, turn, and reverse and continually park,” Dosier suggested.
A shopping cart with a dysfunctional wheel helps everyone to understand the limitations of a swivel caster, which typically must include a small amount of offset distance between the center axis of the vertical shaft and the center axis of the caster wheel. If there is no offset, the wheel will not rotate if not facing the correct direction, either preventing motion or dragging across the ground. Take that same scenario to the industrial and material handling sectors and the exponential growth for the industry standard omniwheel becomes obvious. Rotacaster is both a game-changer and a name-changer.
Thomas R. Cutler is president & CEO of Fort Lauderdale, Florida-based, TR Cutler, Inc, (www.trcutlerinc.com).
Cutler is the founder of the Manufacturing Media Consortium of more than four thousand journalists and editors writing about trends in manufacturing, distribution, material handling, and industry. Cutler can be contacted at trcutler@trcutlerinc.com or 888-902-0300.